Technology
Turbine Nozzle Model
Alloy718
MSXH440R / Power Radius End Mill
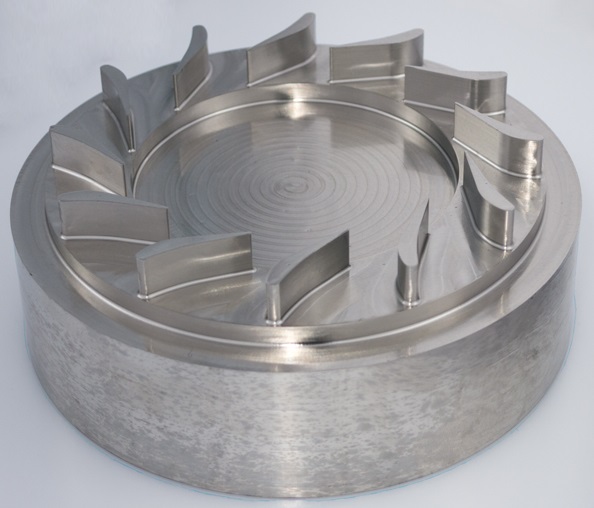
Work Size: Φ80×35(mm)
Material: Alloy718
(Equivalent to Inconel®718)
Cutting time: 1 hr 45 min
Unequal helix angle and flute spacing reduce chattering.
Large tip pocket adopted to realize high efficient milling to tough materials.
Tool
MSXH440R
•Improved designs of unequal helix angle and flute spacing to suppress from chattering to realize stable milling progression.
•Original spiral design at corner radius flutes improves cutting edge performance!
•Designed for high rigidity to suppress corner radius flute breakage even on rough milling stresses.
•Adopted Mugen Coating Premium to suppress from chattering to realize stable milling progression, improved heat resistance and cutting edge strength to protect from milling heat influence.
Cutting Conditions
Cutting part | Outer profile | Inner profile | Blades | Whole | |||
Cutting process | Roughing | Roughing | Finishing | ||||
Helical | Side | Slot | Side | Side | Bottom | ||
Tool | MSXH440R Φ6×R0.5 |
MSXH440R Φ6×R0.5 |
MSXH440R Φ6×R0.5 |
||||
Spindle speed (min-1) |
2,100 | 1,800 | 2,100 | 2,100 | |||
Feed (mm/min) |
500 | 300 | 500 | 300 | 500 | 250 | |
Depth of cut ap×ae(mm) |
8.95×0.2 | ap0.16 | 8.95×0.2 | ap0.6 | 5.95×0.2 | 3~6×0.05 | 0.05×1.5 |
Coolant | Water-soluble fluid | ||||||
Cutting time | 15 min | 20 min | 50 min | 20 min |
Comment
Utilized 2 tools for roughing and 1 tool for finishing in this machining.
Realized high efficient and stable milling to tough material of the heat resistant alloy by using MSXH440R, MUGEN-COATING PREMIUM, spiral shaped corner-R, unequal helix angle and flute spacing.