Technology
MMTS S1.4チタン合金めねじ加工
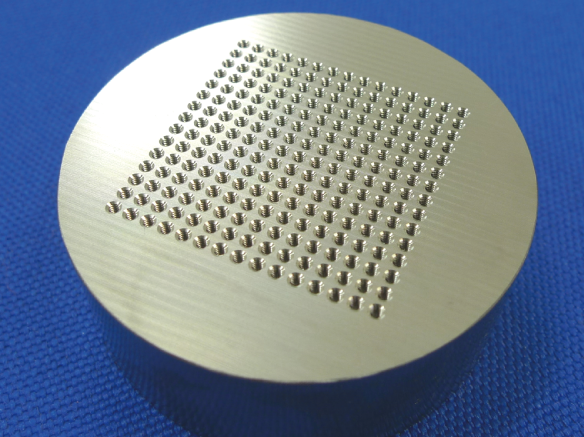
被削材 : Ti-6Al-4V
加工深さ : 3mm
クーラント : オイルミスト
加工時間 : 10秒/1穴
使用工具
MMTS
●世界最小、呼び径0.1mmの、めねじ加工が可能。
●ヘリカルにねじ切り加工を行い、下穴径よりも工具径が小さい為、折損時は取り出し・再加工が可能。
●無限コーティングの採用により長寿命化を実現。
切削条件
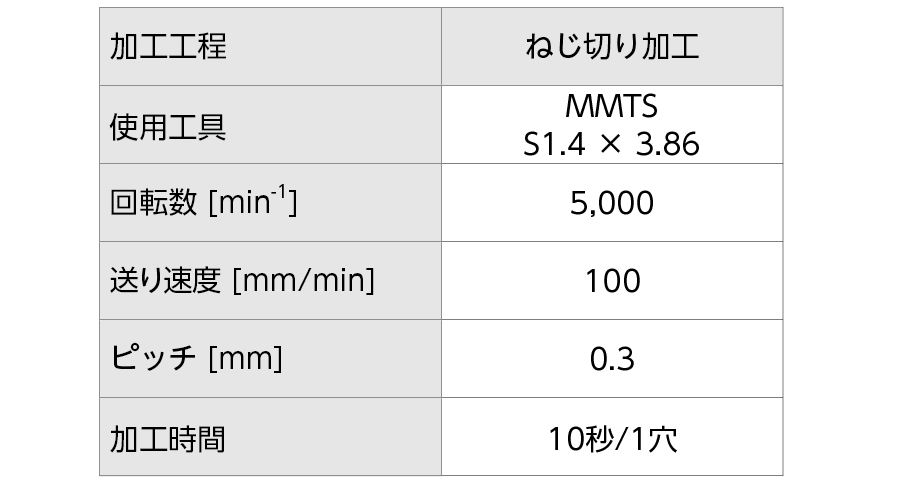
加工結果
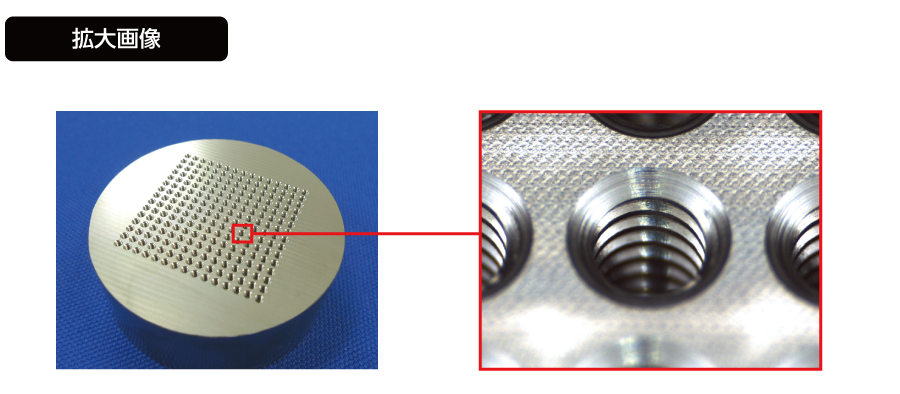



日進工具の大きな強みである微細なサイズをねじ切り工具で実現しました。ミニチュアねじのJIS規格にはない、S0.1とS0.2を日進工具オリジナル規格として標準化!
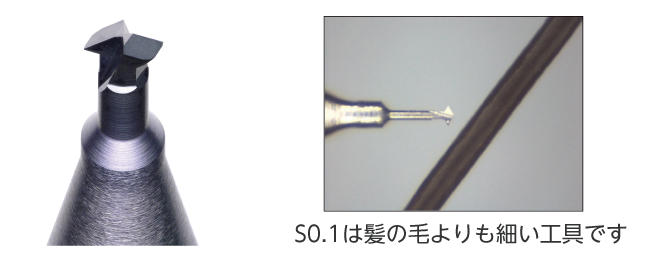

一般的に、ねじの加工としては、おねじの場合は鍛造や旋削加工、めねじの場合はタップを使用した加工が行われています。タップには切削タップや転造タップなどの種類がありますが、共通した問題点として挙げられるのが、タップの折損です。タップが折損すると加工中のねじ穴に工具が詰まってしまい、再加工するのが容易ではありません。このような背景から、最近では、マシニングセンタに専用工具を取り付け、切削加工によりねじ加工を行うスレッドミーリングという方法も多くとられています。この場合、穴径よりも工具が小径であるため、加工中に工具が折損しても容易に取り出すことができ、切削負荷が小さいため高硬度鋼や難削材への高精度な加工が可能になります。
今回開発した製品も、このスレッドミーリング用工具となります。本工具により、S0.1(呼び径0.1mm)のおねじ及びめねじの加工が可能になります。被削材としては、樹脂やアルミニウム合金に加え、医療機器や宇宙・衛星関係機器で多く使われるステンレスやチタンにも対応しています。さらに、大きな特徴として、特殊な機器は必要なく、一般的に使用されている高速マシニングセンタで使用することができます。
一般的に、微小部品の結合には接着剤が使われることが多いですが、医療機器など部品の落下や故障が許されない箇所には、保険として必ず1箇所はねじ止めがされています。機械設計上、ねじのサイズに応じた取り付けスペースを確保しなくてはならず、必然的に製品もそれに合わせたサイズになってしまいます。そのため、ねじを小さくすることで製品のコンパクト化につながるのです。
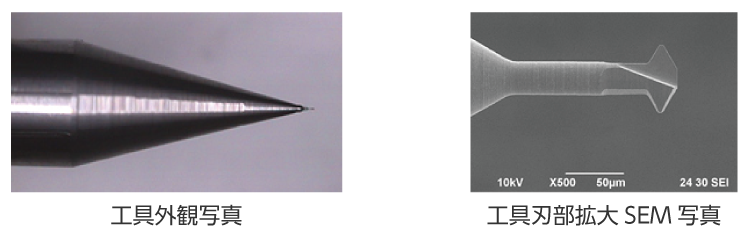

世界最小の直径0.1mmのおねじ、めねじを切削加工するために、工具は外径60μm、首径30μm、有効長150μmの極小径サイズです。一般的に、髪の毛の太さが80μmといわれているため、それよりも細い工具といえば、その小ささをイメージしていただけるのではないでしょうか。極小径サイズの超硬エンドミル、cBNエンドミル、超硬ドリルを得意とし、既に最小外径10μmのエンドミルも世界で初めて量産化に成功している弊社ならではの知識と経験により、本工具の開発を実現しました。

純チタン(2種)に対して行っためねじ加工。工程として、R30μmのボールエンドミルでドリルのセンター穴をあけ、次にφ70μmのドリルで穴をあけます。最後に本工具でねじ山を切削加工しました。
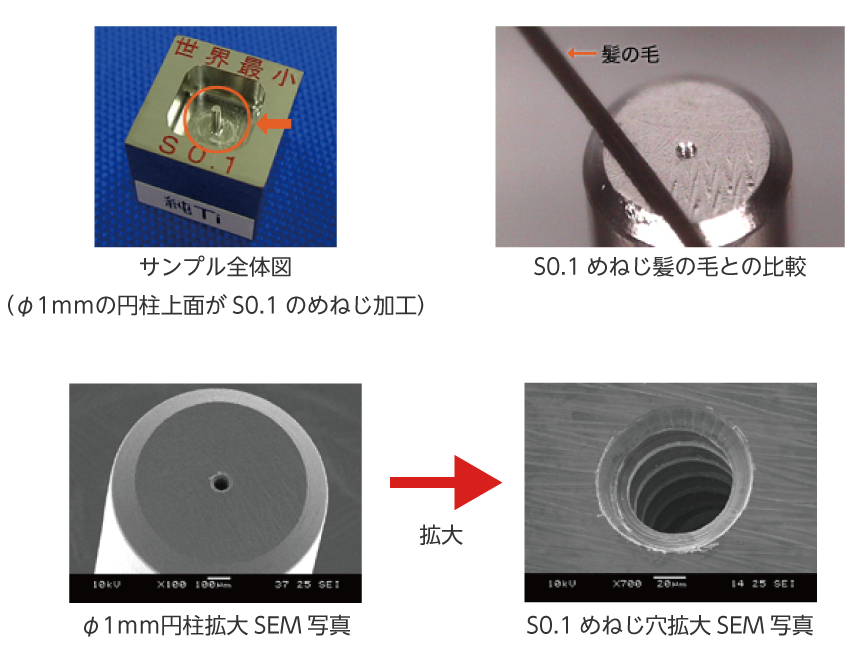
直径1mmの円柱の上面にめねじ加工。バリも小さく、良好な切削面であることがSEM画像から観察できます。加工時間は、ねじ山加工が約30分、下穴を含めて約45分で1穴の加工が出来ました。尚、ステンレス(SUS304)やアルミ(A7075)へ同様の加工を行うことも可能です。
ステンレス(SUS304)に対して行ったおねじ加工では、スクエアエンドミルで直径0.1mmの円柱を削りだし、本工具でねじ山の加工を行いました。
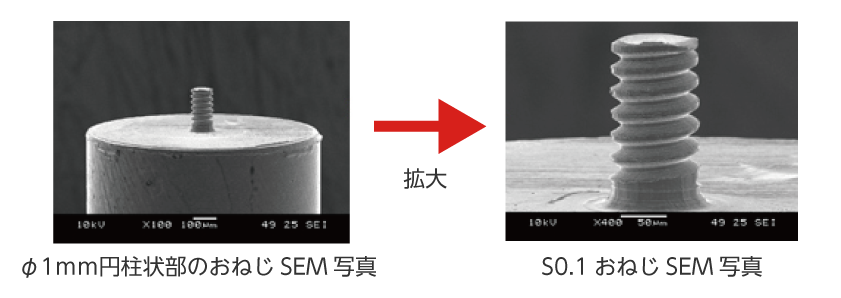
SEM画像を観察すると微小ながらしっかりとしたねじの形状が形成されており、バリも少なく滑らかな切削面であることが分かります。加工時間は、ねじ山加工が約30分、円柱の加工は15分でした。もちろん、先ほどのめねじとの締め付けが可能な加工精度です。
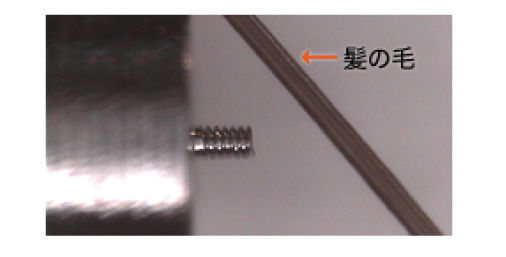

加工に際し特殊な機械を新たに導入する必要はなく、一般的な高速マシニングセンタと本工具があれば可能になります。微細な加工では、レーザー加工やエッチング加工を多く聞きますが、どちらも二次元的な加工を得意としています。近年では、エッチングで三次元形状を製作することが可能になってきていますが、まだ研究段階であり、設備としても数億円と高額なものが多いのが現状です。
さらに、加工時間は下穴など含めたトータルでみても1時間かかりません。これを形彫り放電加工など別な方法で行うと、電極の作成や、形状が微小なため条件を下げた放電加工など多くの時間を要すると思われます。
このように、設備投資、加工コストの観点から、本工具を用いた加工法は極めて有効な手段だといえます。