Technology
SSBL200 複合微細溝形状
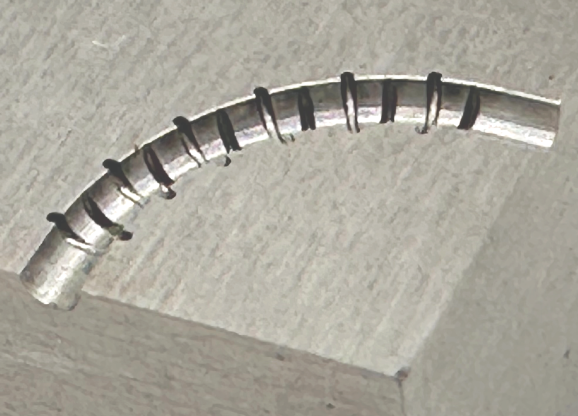
被削材 : K340(60HRC)
ワークサイズ : 15×15×5mm
クーラント : 不水溶性切削油
加工時間 : 5時間55分
使用工具
SSBL200
●深彫り加工に対応。ロングネックタイプをシリーズ化!全25サイズ!
●首下長が10mmまで。より深い加工に対応。
●CBNの長寿命と、ロングネックにより新たな加工領域を実現。
●極小径サイズR0.05から規格化!
●独自の刃形状によりR精度±0.003、耐チッピング性能がUP!
切削条件
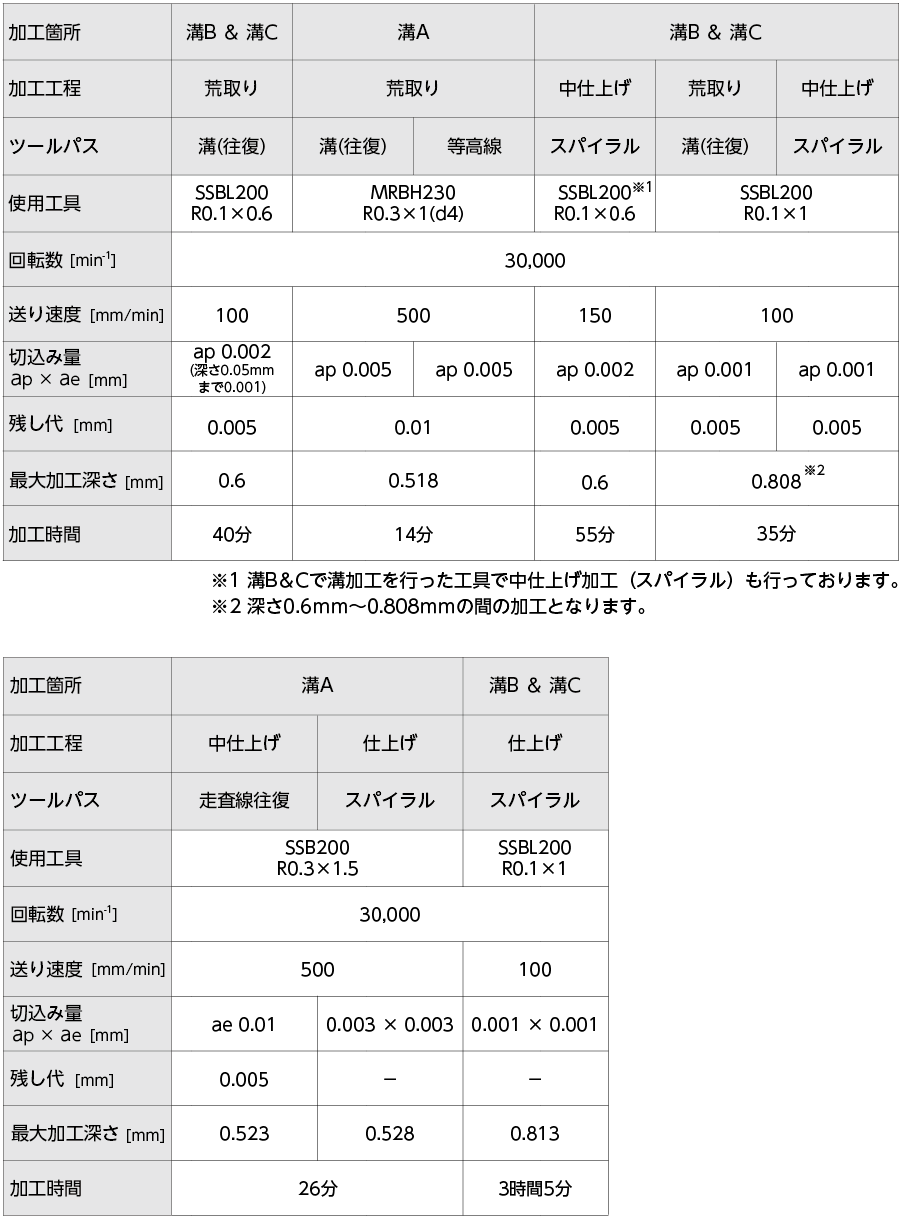
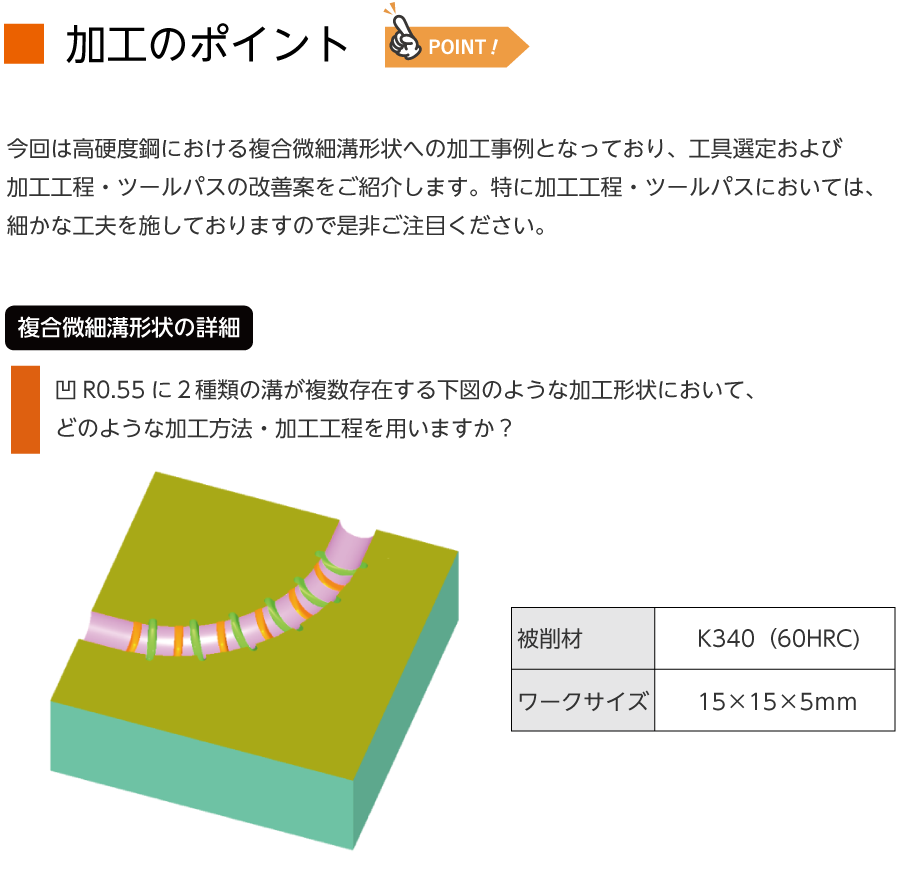
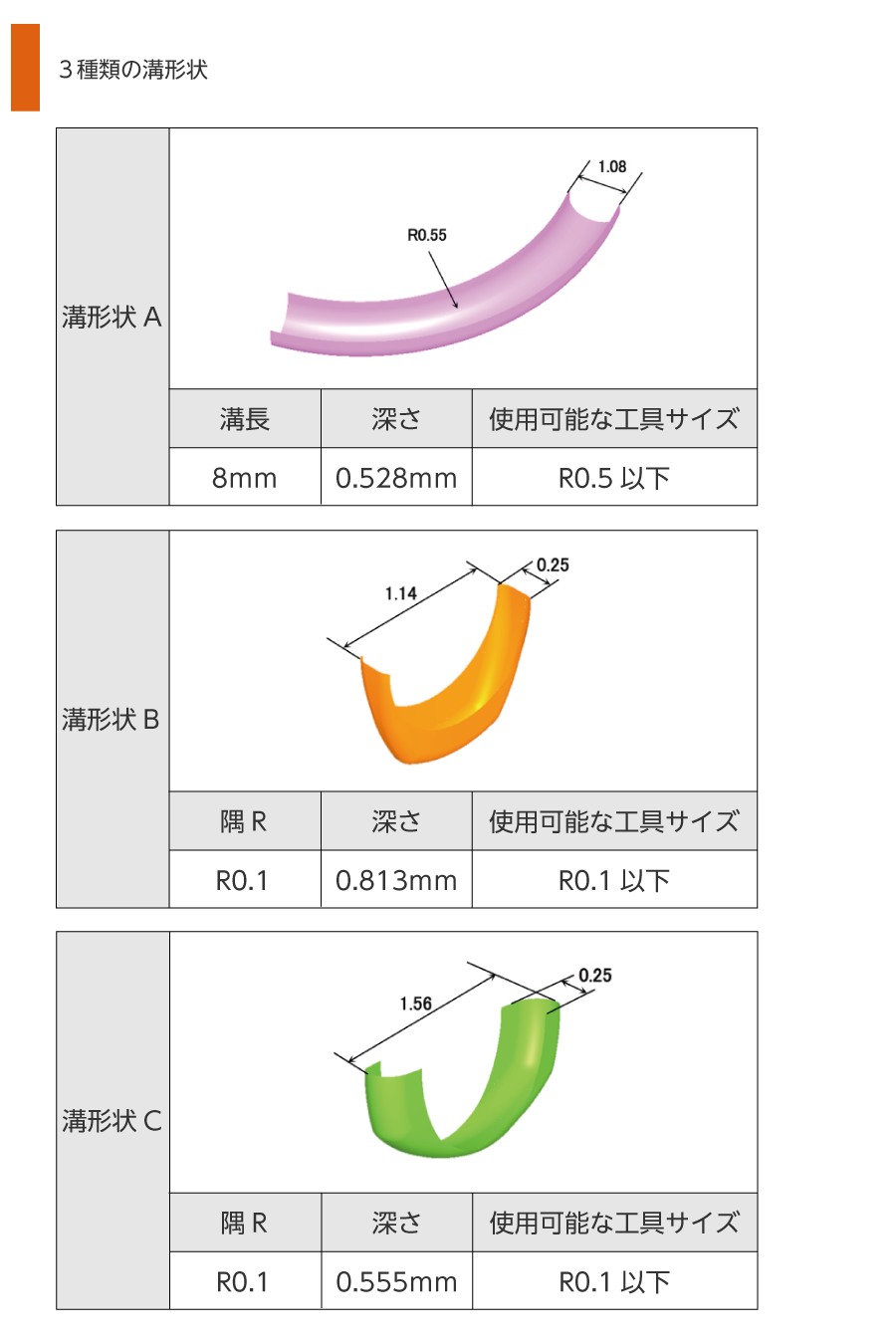
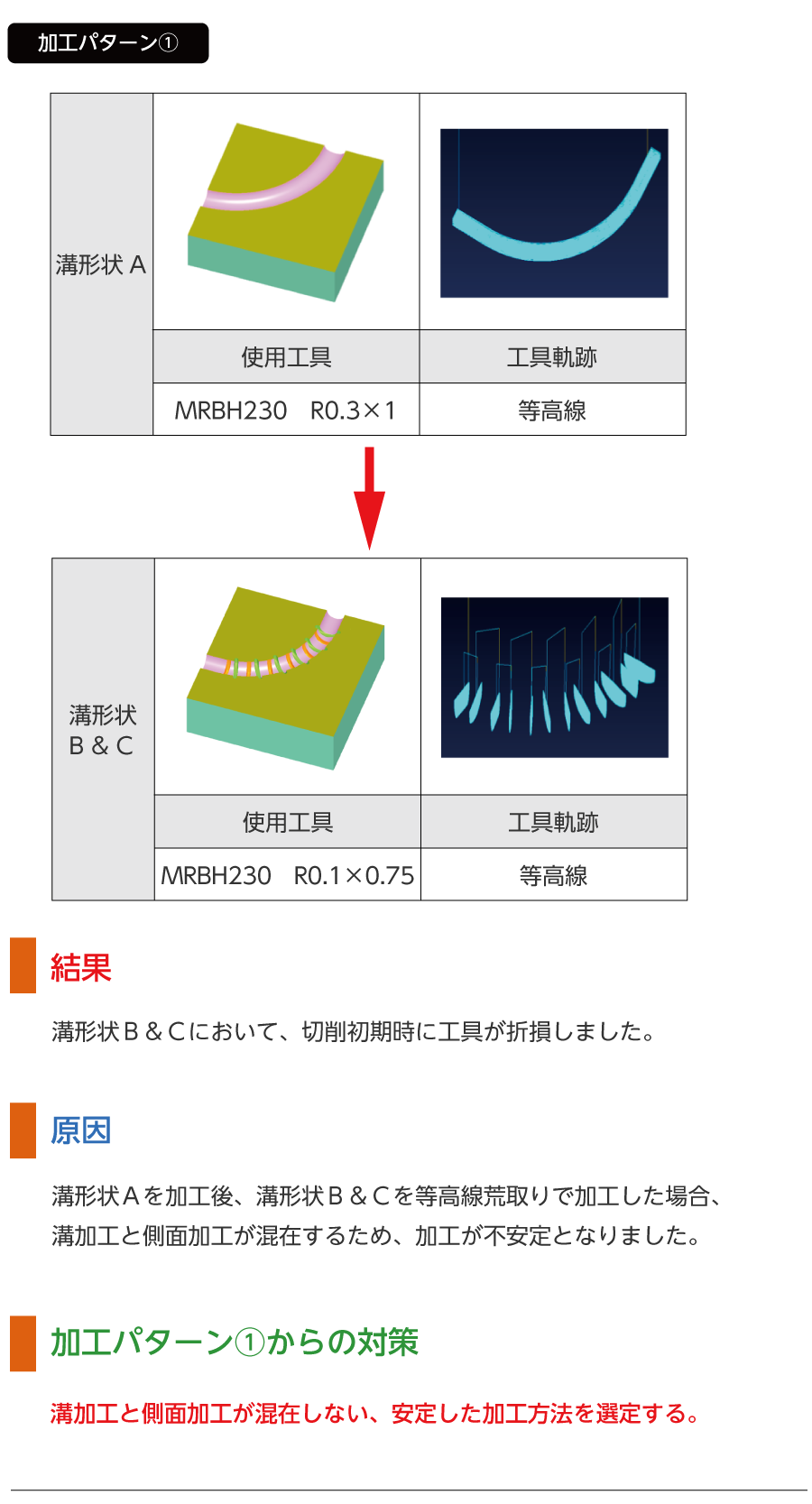
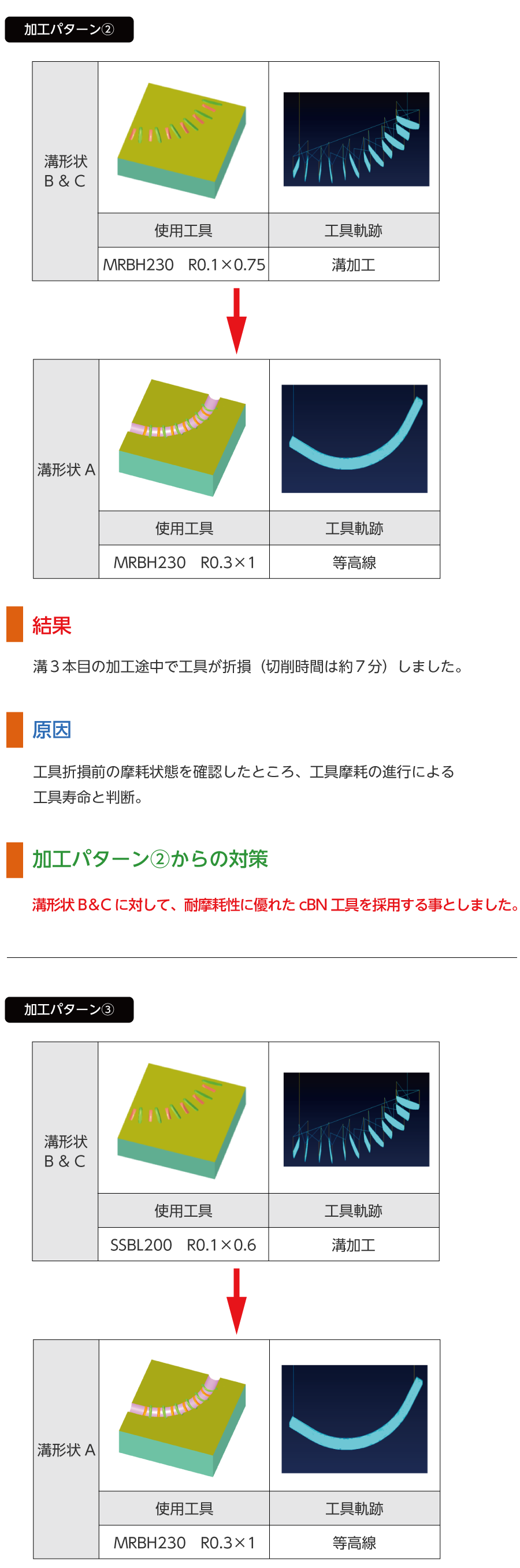
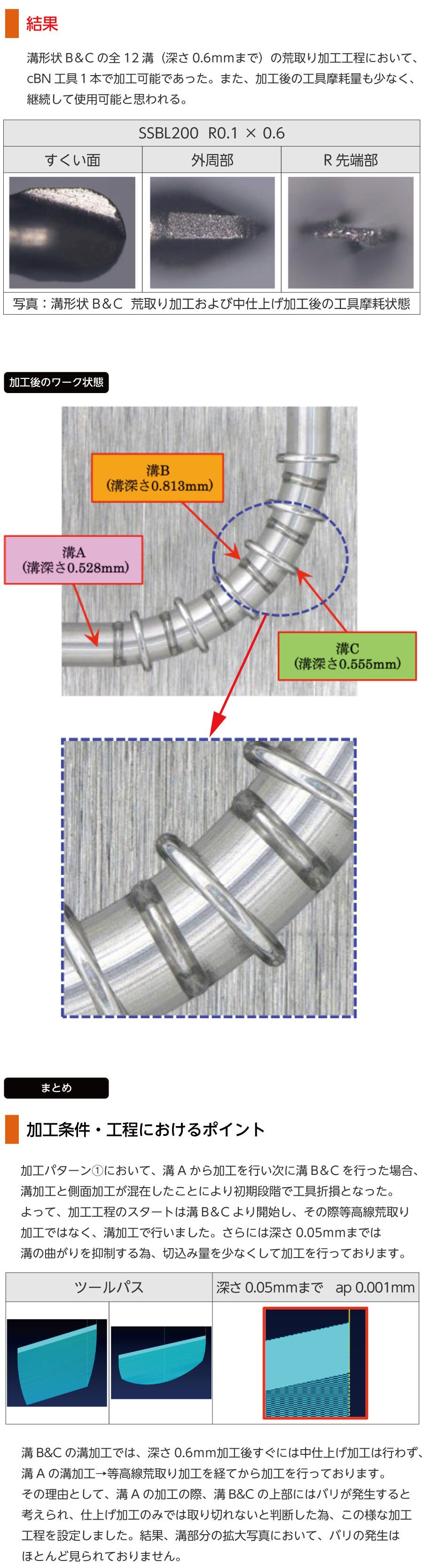

今回は高硬度鋼における複合微細溝形状への加工事例となっており、工具選定および加工工程・ツールパスの改善案をご紹介します。特に加工工程・ツールパスにおいては、細かな工夫を施しておりますので是非ご注目ください。
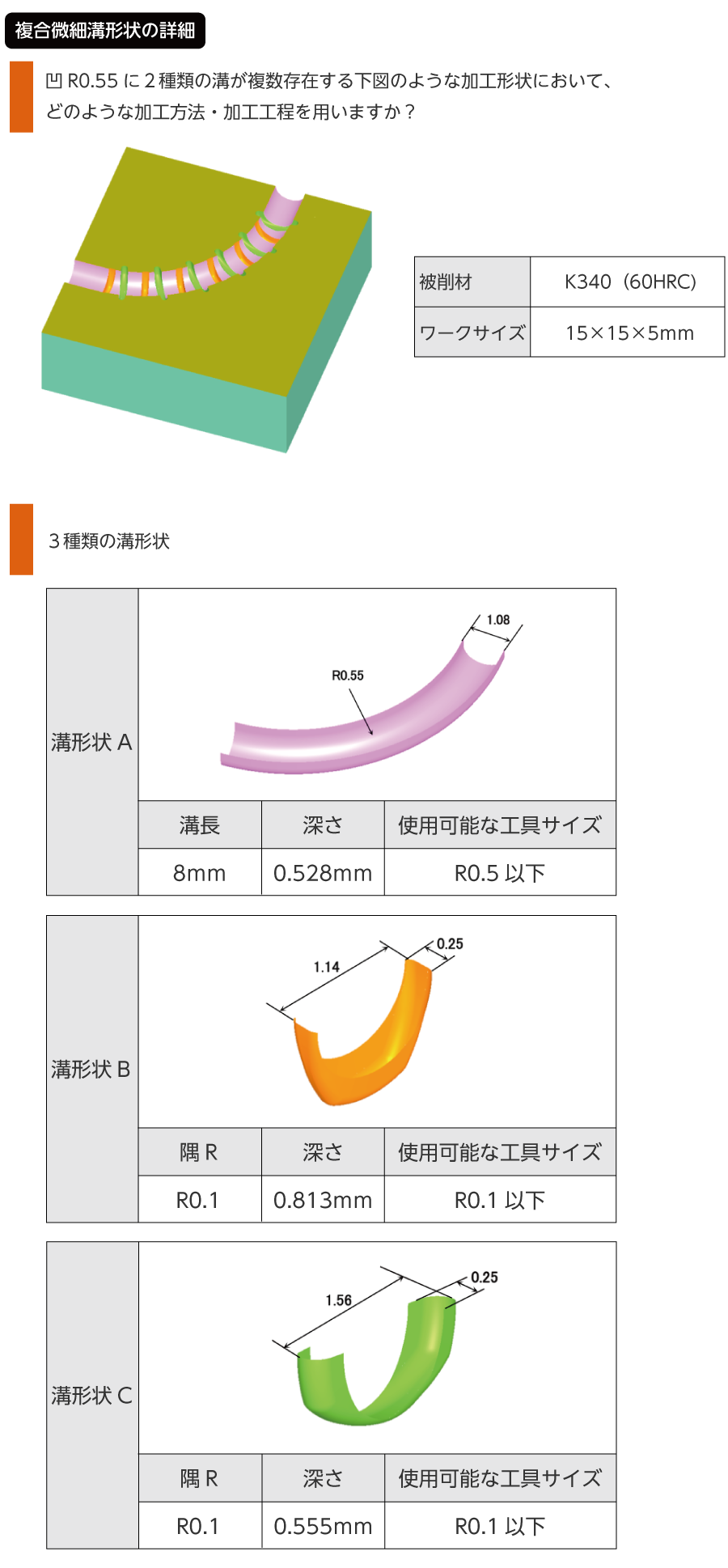
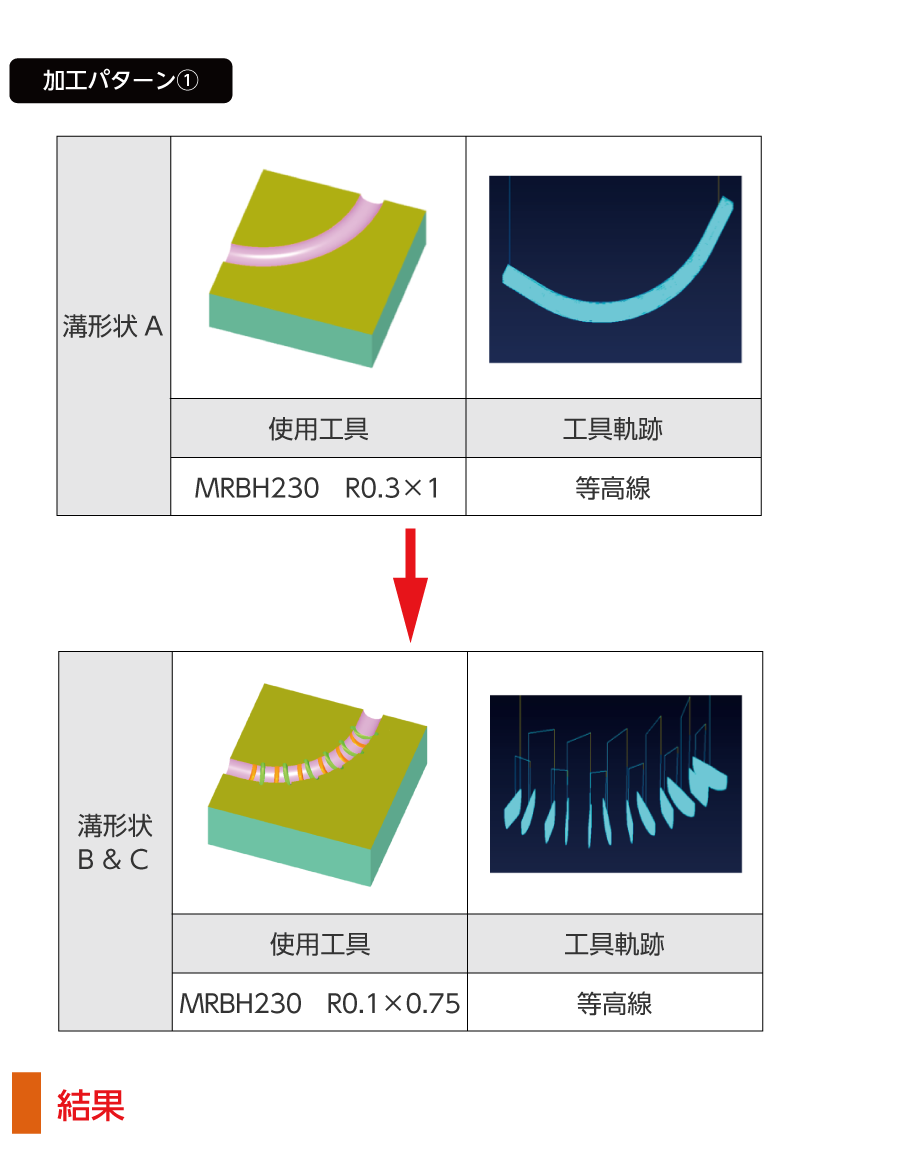
溝形状B&Cにおいて、切削初期時に工具が折損しました。

溝形状Aを加工後、溝形状B&Cを等高線荒取りで加工した場合、溝加工と側面加工が混在するため、加工が不安定となりました。

溝加工と側面加工が混在しない、安定した加工方法を選定する。
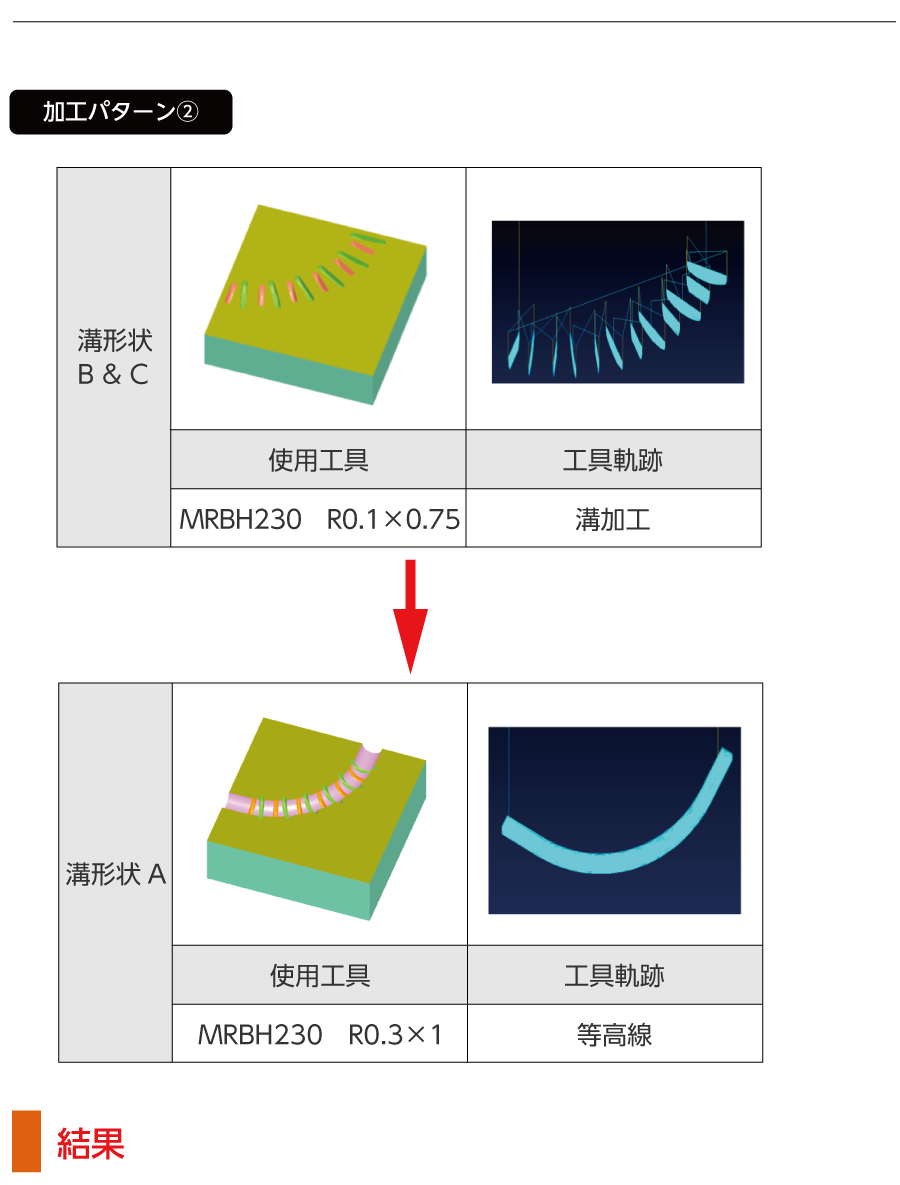
溝3本目の加工途中で工具が折損(切削時間は約7分)しました。

工具折損前の摩耗状態を確認したところ、工具摩耗の進行による工具寿命と判断。

溝形状B&Cに対して、耐摩耗性に優れたcBN工具を採用する事としました。
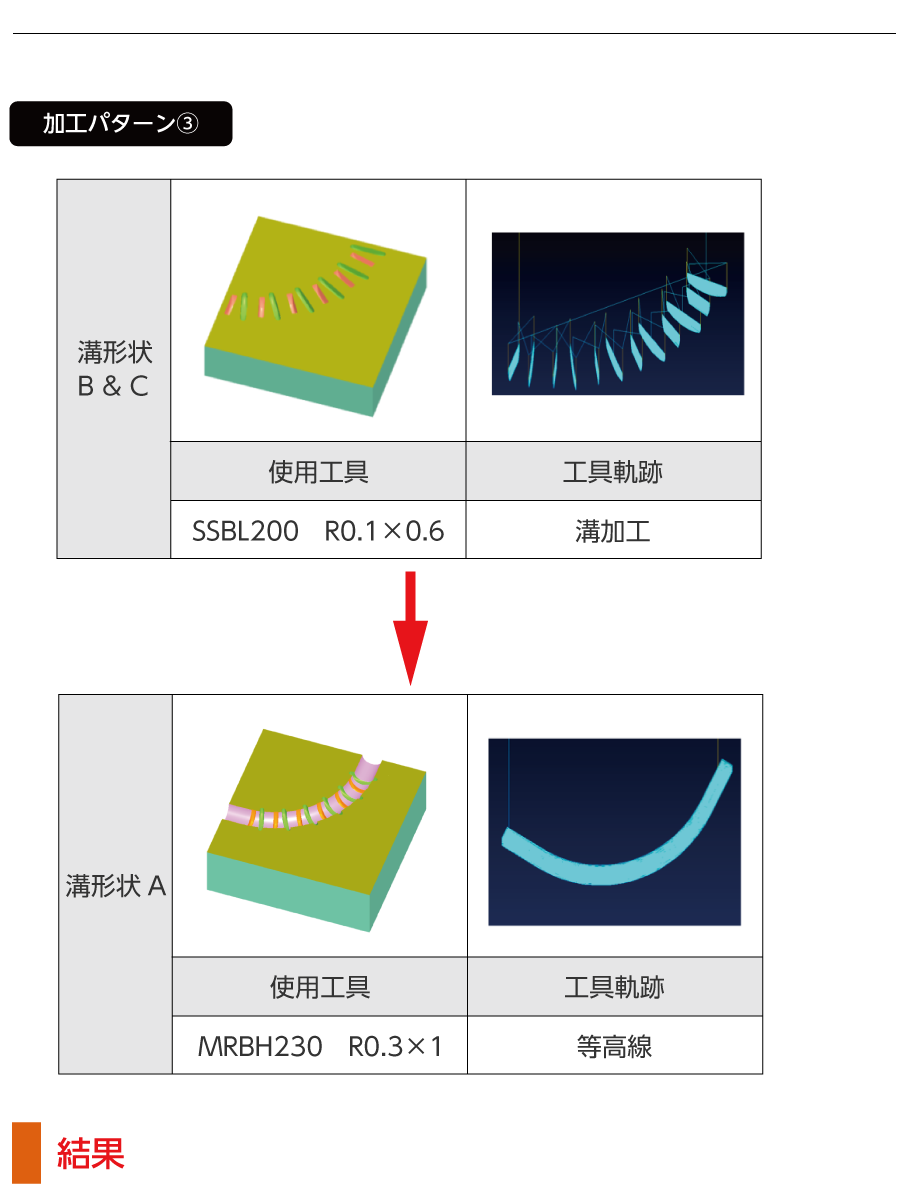
溝形状B&Cの全12溝(深さ0.6mmまで)の荒取り加工工程において、cBN工具1本で加工可能であった。また、加工後の工具摩耗量も少なく、継続して使用可能と思われる。
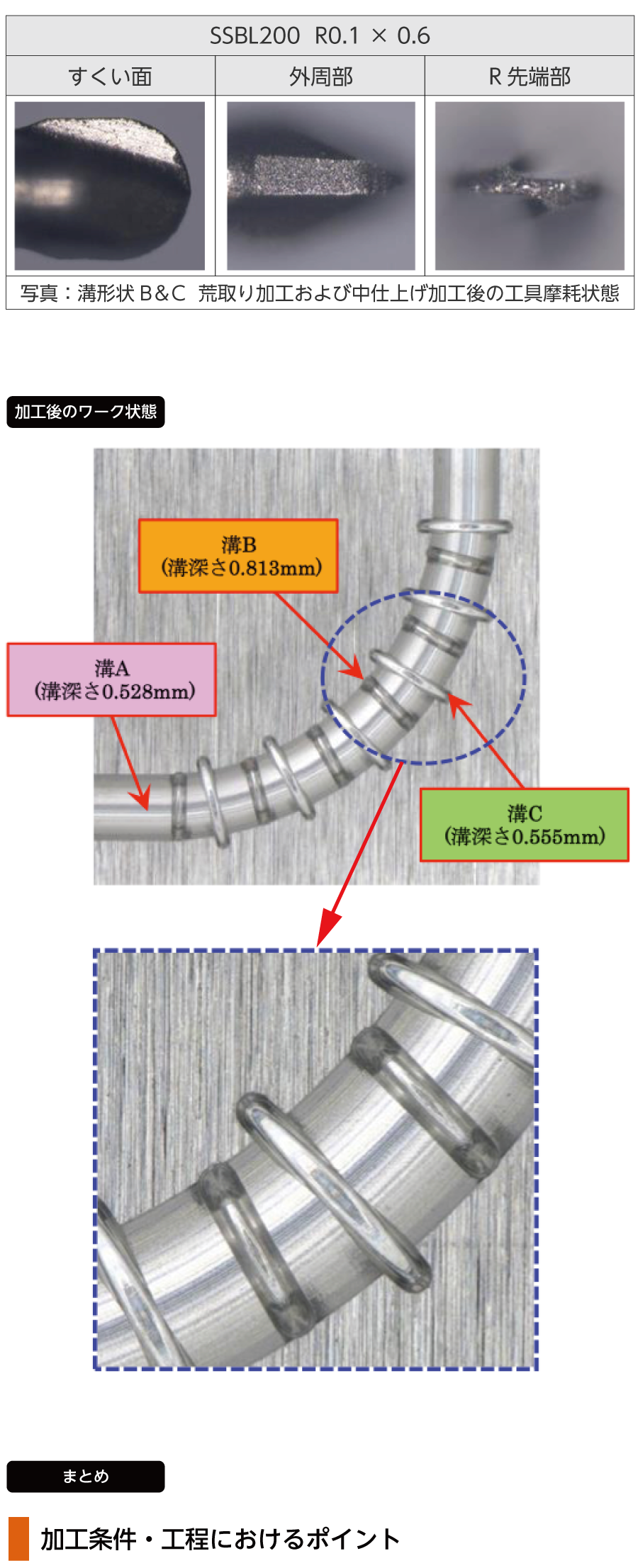
加工パターン①において、溝Aから加工を行い次に溝B&Cを行った場合、溝加工と側面加工が混在したことにより初期段階で工具折損となった。よって、加工工程のスタートは溝B&Cより開始し、その際等高線荒取り加工ではなく、溝加工で行いました。さらには深さ0.05mmまでは溝の曲がりを抑制する為、切込み量を少なくして加工を行っております。
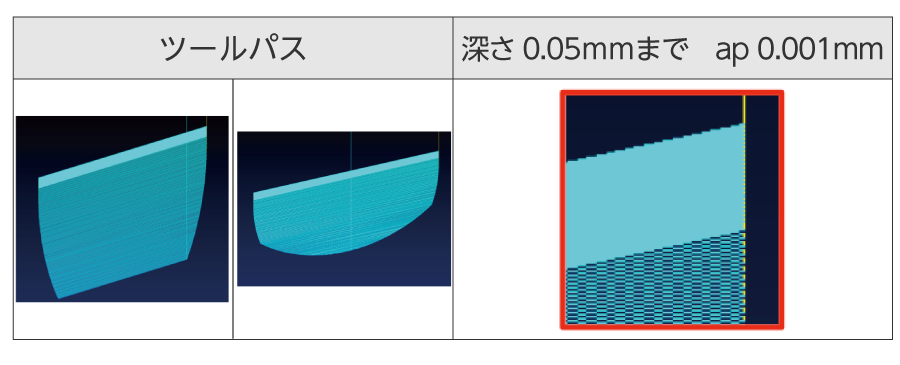
溝B&Cの溝加工では、深さ0.6mm加工後すぐには中仕上げ加工は行わず、溝Aの溝加工→等高線荒取り加工を経てから加工を行っております。その理由として、溝Aの加工の際、溝B&Cの上部にはバリが発生すると考えられ、仕上げ加工のみでは取り切れないと判断した為、この様な加工工程を設定しました。結果、溝部分の拡大写真において、バリの発生はほとんど見られておりません。