Technology
MRBSH230SF ギヤ形状パンチサンプル
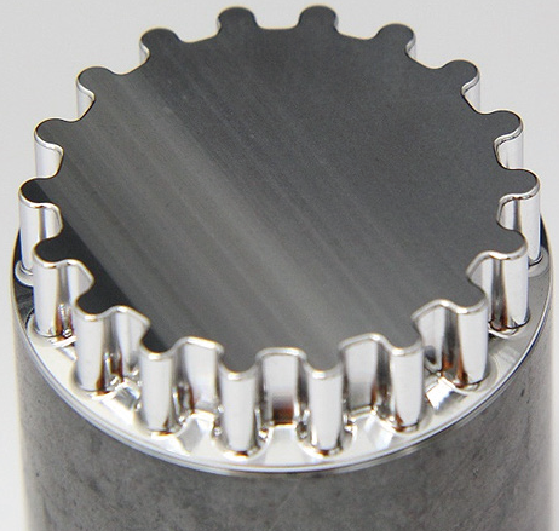
被削材 : HAP40(65HRC)
ワークサイズ : Φ25 × 60mm
加工深さ : 6mm
クーラント : オイルミスト
加工時間 : 8時間46分
使用工具
MRBSH230SF
●70HRCの高硬度鋼でも長寿命で安定した切削性能を実現。
●新たに無限コーティングプレミアムPlusを開発、耐酸化性・耐摩耗性が向上。
●耐欠損性を向上させた新素材と切削負荷を低減する切れ刃形状を採用。
●R精度は±0.003mm(R精度は実外径の1/2を基準とする)。
●シャンク径公差は -0.001mmから -0.003mmの高精度仕様。
切削条件
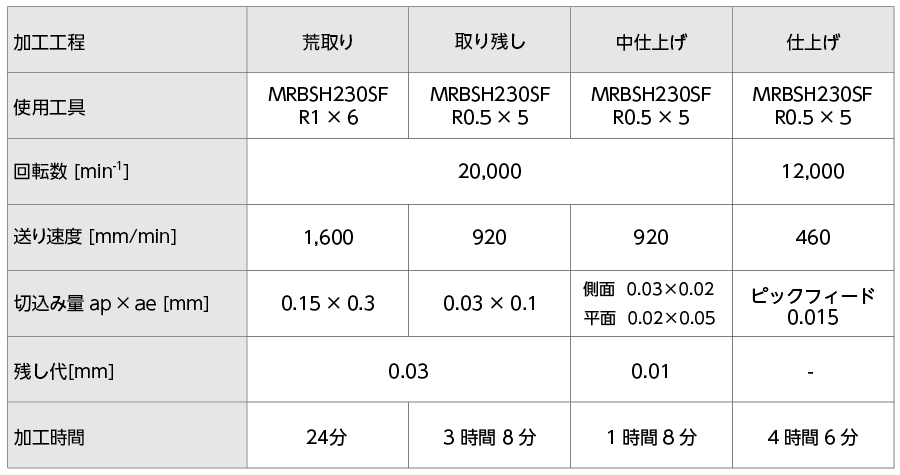
加工結果
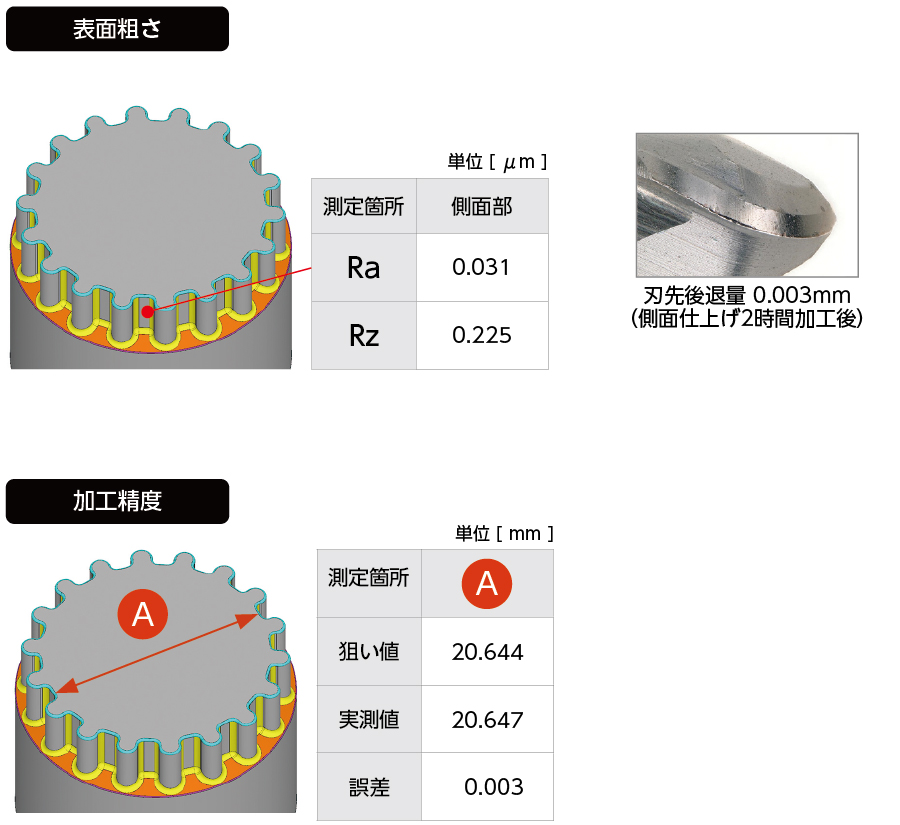
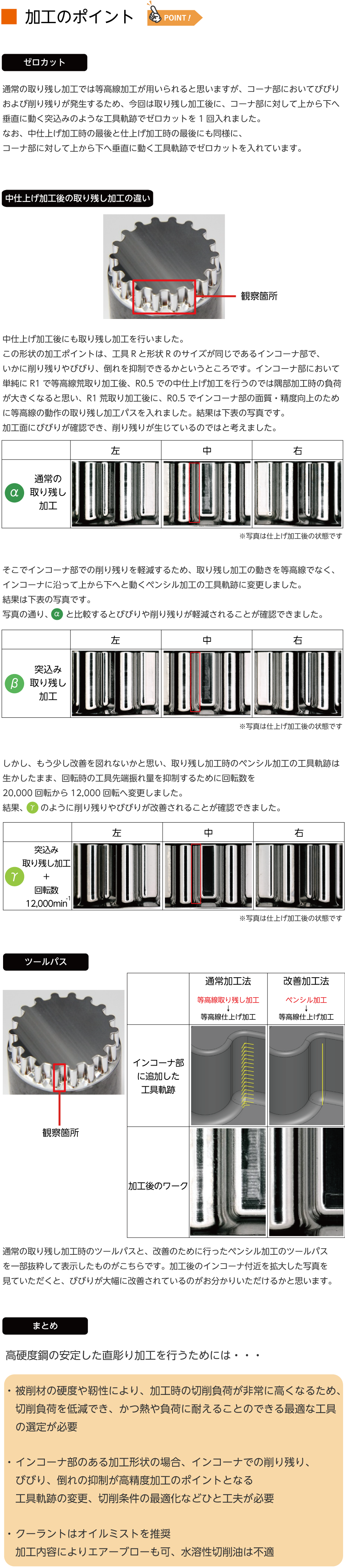

通常の取り残し加工では等高線加工が用いられると思いますが、コーナ部においてびびりおよび削り残りが発生するため、今回は取り残し加工後に、コーナ部に対して上から下へ垂直に動く突込みのような工具軌跡でゼロカットを1回入れました。なお、中仕上げ加工時の最後と仕上げ加工時の最後にも同様に、コーナ部に対して上から下へ垂直に動く工具軌跡でゼロカットを入れています。
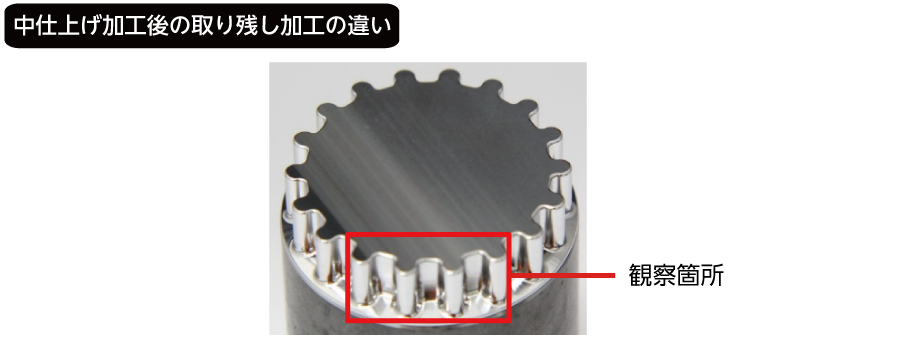
中仕上げ加工後にも取り残し加工を行いました。この形状の加工ポイントは、工具Rと形状Rのサイズが同じであるインコーナ部で、いかに削り残りやびびり、倒れを抑制できるかというところです。インコーナ部において単純にR1で等高線荒取り加工後、R0.5での中仕上げ加工を行うのでは隅部加工時の負荷が大きくなると思い、R1荒取り加工後に、R0.5でインコーナ部の面質・精度向上のために等高線の動作の取り残し加工パスを入れました。結果は下表の写真です。加工面にびびりが確認でき、削り残りが生じているのではと考えました。
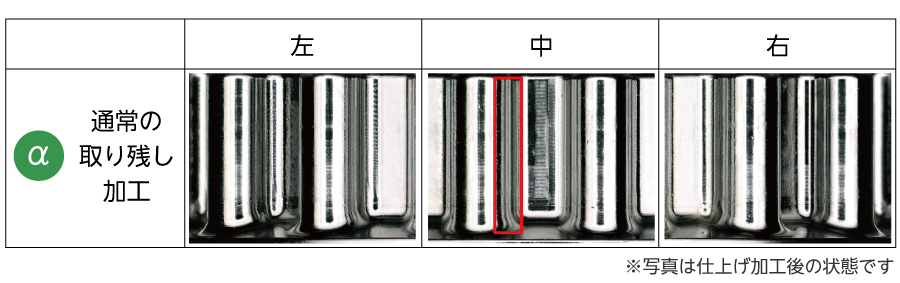
そこでインコーナ部での削り残りを軽減するため、取り残し加工の動きを等高線でなく、インコーナに沿って上から下へと動くペンシル加工の工具軌跡に変更しました。結果は下表の写真です。写真の通り、通常の取り残し加工と比較するとびびりや削り残りが軽減されることが確認できました。
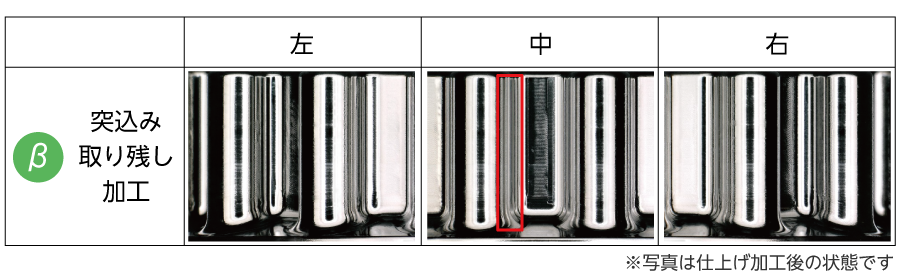
しかし、もう少し改善を図れないかと思い、取り残し加工時のペンシル加工の工具軌跡は生かしたまま、回転時の工具先端振れ量を抑制するために回転数を20,000回転から12,000回転へ変更しました。結果、下表の写真のように削り残りやびびりが改善されることが確認できました。
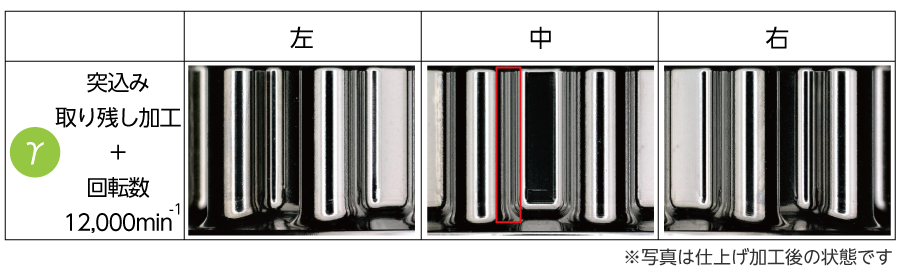
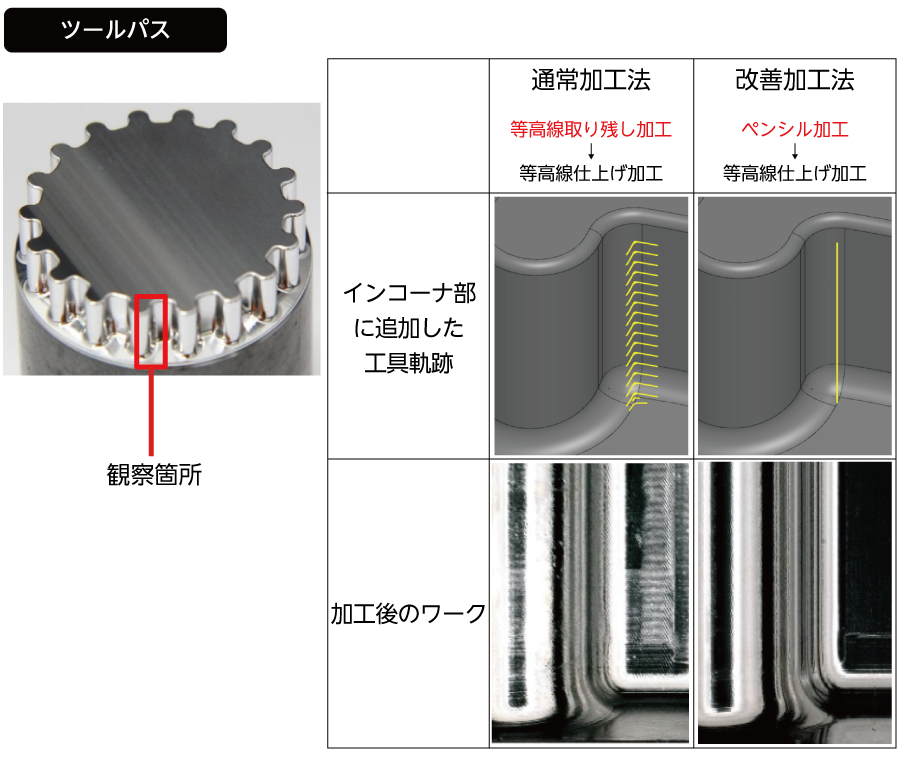
通常の取り残し加工時のツールパスと、改善のために行ったペンシル加工のツールパスを一部抜粋して表示したものがこちらです。加工後のインコーナ付近を拡大した写真を見ていただくと、びびりが大幅に改善されているのがお分かりいただけるかと思います。

高硬度鋼の安定した直彫り加工を行うためには・・・
・ 被削材の硬度や靭性により、加工時の切削負荷が非常に高くなるため、切削負荷を低減でき、かつ熱や負荷に耐えることのできる最適な工具の選定が必要
・ インコーナ部のある加工形状の場合、インコーナでの削り残り、びびり、倒れの抑制が高精度加工のポイントとなる工具軌跡の変更、切削条件の最適化などひと工夫が必要
・ クーラントはオイルミストを推奨加工内容によりエアーブローも可、水溶性切削油は不適